Normal
0
false
false
false
EN-US
X-NONE
X-NONE
...
Wednesday, 12 July 2017
Basic Concept of LEAN Methodology
Posted by Advance Innovation Group on 06:37 with No comments
Posted in Lean Training, Online Lean Program, Online Lean Training
Subscribe to:
Posts (Atom)
Popular Posts
-
By the Oxford dictionary when we use the term Lean as an adjective for a person or animal it means that person or animal is thin, es...
-
Advance Innovation Group Background Advance Innovation Group has been an industry leader in the consulting and training space in ...
-
It’s a factory of Knowledge, Thoughts, Ideas, Innovation, Analytics, Quality metrics and so on…. All these key ingredients make us the “...
-
Nurturing a talent is something we have mastered over the years. From the day, you become our student till you complete your training ...
-
The course has been designed to be completed in 16 hours. · 16 hours of high quality instructor led training · ...
-
In the day to day work, when we talk about “Defining” something it infers to creating a detailed description or a checklist to achieve ...
-
“You don’t need to push through a Sale, if your product / service is good enough – Sale will happen without any efforts” Un like o...
-
ITIL Overview ITIL offers a commonly established approach to managing business and IT services. ITIL comprises best IT practices that inc...
-
Six Sigma is power-driven by principles which are governed by nonstop improvement. In pure terms, Six Sigma help industrialized organizati...
-
The training and certification of Big Data have come up with a surplus of opportunities. They play a vital role in enabling the professi...
Blogger templates
Blogroll
Categories
- 7 QC tool – Histogram
- Advance Innovation Group
- Advance innovation group Noida
- advance innovation group reviews
- Agile Expert Certified Program
- Big Data Certification Noida
- Big Data Training
- Big Data Training Noida
- Control Communications
- DMAIC Methodology
- E-Learning facility
- Hadoop Certification Training
- Hadoop Training
- Hadoop Training Noida
- ISO 27001 Online Training
- ISO 9001 Training
- ISO Programs Excel Training
- ISO Training
- ITIL Certification
- ITIL foundation training
- ITIL Training
- Lean Consulting
- lean six sigma black belt certification
- Lean Training
- Minitab
- MSA Training
- Net Promoter Score
- Online Lean Program
- Online Lean Training
- Online Six Sigma Program
- Online Six Sigma Training
- PMP certification
- Prince2 certification
- Prince2 Training
- Project Management
- Project Management Training
- Scrum Master Certified Program
- six sigma black belt
- Six Sigma Consulting
- Six Sigma Consulting Six Sigma Process Process Improvement Consultant
- Six Sigma methodology
- six sigma program
- Six Sigma Training
- Six Sigma training and Certification
About Me
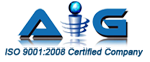
- Advance Innovation Group
- Six Sigma Provide E-learning program courses such as black belt, green belt and yellow belt etc.
Blog Archive
Powered by Blogger.